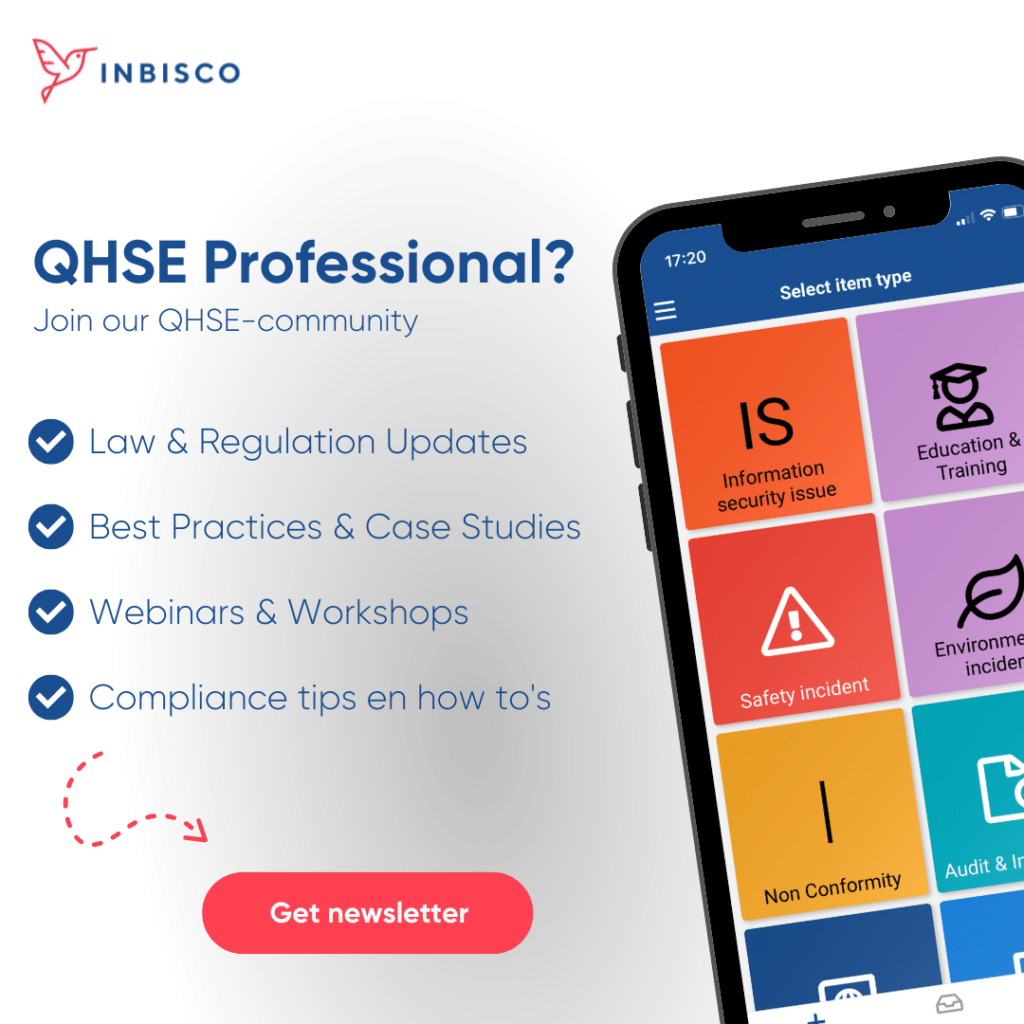
INBISCO QHSE Community
8 Oct 2024
Continuous improvement; these are two words that not only appear frequently on our website but are also very important words within quality management. Continuously improving your organization is the desired end result of effective quality management! That is why we have created a step-by-step plan in this blog that will help you bring your organization into a cycle of continuous improvement.
First, it is useful to look at what Continuous Improvement actually means. Continuous improvement means, very obviously, that you want to lift your organization to a higher quality level. Namely, a level where the entire culture and working method is set and motivated to continuously improve the quality within each business process. In doing so, you hope to make your production chain or service more efficient and save on costs and time. Originally, continuous improvement is part of so-called ‘Lean Management’, a form of management in which the entire organizational chain revolves around creating maximum value for the customer. However, we believe that all stakeholders of an organization should be able to benefit from this maximum value, not just the customer. Ultimately, the basis of Continuous Improvement for us lies in two important points. On the one hand, it lies in the culture and the people within your organization and on the other hand, it lies in the implementation and use of a good quality management system.
With Continuous Improvement within your organization, the employee is central. Now I hear people say ‘the employee is usually central, otherwise your organization cannot function properly’. However, over the years we have forgotten how important the input of employees is in improving your organization. If you look at the collective intelligence of all your employees together, there is a valuable source of inspiration and motivation for improvement! Everyone is different, works in a different way and has different tasks and responsibilities. This not only provides different perspectives but also many eyes that look together at your entire business operations.
With Continuous Improvement you use this collective intelligence and attentiveness and motivate all your employees to report and implement improvements in all business processes. These can be improvements of any size. Because you stimulate all your employees to constantly come up with (small) improvements, you can continuously improve the many aspects of your business operations; such as costs, quality, work safety, productivity, customer contact, etc. This way of improving within your organization is very efficient and provides, among other things, more motivation to work harder because people see that effort has a visible effect. This is also where management has a responsibility. If you do not let this continuous improvement culture flourish, you will miss out!
To ensure that all your employees can report their improvement points, it is of course most useful to have a system that registers this in a structured and systematic manner and can analyse and monitor these points. You do not want everyone to keep track of improvements in Excel or Word files, it is important that this is done transparently and effectively. For this you need a quality management system. A good quality management system ensures that everyone within your organisation can register, analyse, improve and monitor these reports.
1. Take a good look at why you want to implement continuous improvement in your organization: In this first step, it is important that you take a good look at the mission, vision, values and goals that you have set as an organization. It is important that this step fits within your organization and that it strengthens your mission, vision, values and goals.
2. Reflect on who (which stakeholders; both inside and outside the organization) you want to involve in continuous improvement within your organization and what your motives are for taking this step: Before you start implementing a quality management system, we recommend that you take a good look at which stakeholders you want to involve. By this we mean that you should take a good look at which stakeholders (employees, customers, etc.) you integrate into your quality management system and therefore let help you improve your quality. In addition, it is important that you take a good look at the goals you want to achieve in the field of continuous improvement. This gives you something to strive for. Look at certain goals that you want to achieve in your service, or certain ISO certifications that you want to obtain, etc.
3. Implement a good quality management system: We have already discussed that a quality management system is incredibly helpful in implementing Continuous Improvement within your organization. We therefore recommend that every organization actually implement such a system when the decision has been made to focus more on quality.
4. Make sure that everyone understands the system well: This part is crucial for continuous improvement, because if your system does not land well within your organization, your investment will be of little use. So make sure that you purchase an accessible quality management system and implement it well with a lot of personal attention for your employees. Then set up the system well (with help) so that everyone knows how, what and where they can report their improvements. Think about the different departments within your organization, but emphasize that people should not limit themselves to their own department with improvements. Above all, show the value of the quality management system for both your employees and the entire organization.
5. Register: Once you have implemented your system, the real work begins; registering deviations and improvements. Step 4 is therefore crucial to motivate people to actually pay attention and to encourage them to dare to register real improvements in step 5. With a quality management system, you create a valuable data pool via these registrations that you can use to analyze your quality process.
6. Analyze: By registering all deviations, you can analyze this collected data in a good quality management system and see where quality problems lie within your organization. This data is very valuable because it also provides a good picture of what is happening within your organization.
*At INBISCO, all employees can register and assign deviations, improvements and tasks in our quality system IRIS. This way, you always have real-time information about what is happening within your organization, you can perform analyses at any time and act immediately.
7. Realize solutions: When deviations, tasks or quality improvements are registered, it is of course useful if someone can immediately start working on these reports. In a good quality system, it is therefore useful if you can immediately assign tasks to people within such a report so that the quality can be improved immediately. So when a report comes in, it is advisable to immediately link people to it who can realize the solutions. In this way, you tackle quality problems immediately and it becomes easier to continuously improve.
8. Monitor: When solutions for reports are planned, it is wise to monitor them and see the progress of such an improvement process.
9. Report: When many deviations and/or improvements have been reported within a certain branch of your organization, it is of course good to make reports of this in between in order to analyze the progress of the quality improvements within your organization and to report these to the person responsible for the entire improvement process. These reports can help to control the entire process, create an overview of the progress and coordinate tasks and responsibilities.
10. Evaluate and steer: Once reported, you can evaluate the final improvements, reflect on how the process went, and use the new insights to adjust your strategy and business processes to take your organization to the next level.
11. Repeat from step 6 for the continuous improvement cycle. When steps 6 to 10 go smoothly and become the new normal within your organization, you have truly implemented continuous improvement within your organization. It remains important to continue to reflect on how this entire process is going, because you can also continue to improve with continuous improvement!
Do you want to take your organization to a new level of quality? At INBISCO we offer the quality management system (IRIS) that can help every organization to implement continuous improvement throughout the entire business operations. Interested? Please contact us and/or request a free demo!
Here you will find our latest blogs, events, online demonstrations and customer stories. Stay up to date with the latest developments and be inspired by practical examples in the field of quality, health, safety and environment.