First: Quality Management
Before you can talk about a quality management system, you need to know what quality management entails. Quality management concerns all business units that are concerned with improving, controlling and managing the quality within your company. When you think of quality, you should think of all processes within your company that have to do with the quality of your products, the quality of your service, the quality of your work environment, your processes, etc.
What is a quality management system?
A quality management system (also known as QMS) is a system that helps you to systematically, transparently and effectively guarantee the quality of your entire business operations and to bring them into a process of continuous improvement. A quality management system can be seen as a kind of Business Process Management system, since with a quality management system you automate, analyze, monitor and improve quality processes within an organization.
A quality management system is not just purchased, of course it is purchased because you, as a quality manager or consultant, want to improve the performance of the organization in question. With the right system you can better guarantee your quality for your customers, make your quality management system more efficient and transparent and it becomes easier to meet all requirements and conditions regarding quality management. Enough reasons to get started with such a system!
Why a Quality Management System?
As mentioned above, there are many benefits to purchasing a quality management system for both inside and outside your organization. Some of the benefits of implementing such a system are:
- You increase your quality: This is of course the most obvious benefit. With a quality management system, you increase the quality of all your quality processes. With the help of a system, you give your quality managers a tool that helps them to perform their work more easily, efficiently and safely.
- You reduce the number of complaints about quality: Every organization has complaints from customers about quality at some point. However, if you register, analyze and address complaints from your employees or customers immediately after they have been made, you can immediately resolve them and take measures to avoid and prevent these complaints in the future. When the cause, the improvement measures and the consequences are clear and registered in a system, you get a better picture of where the complaints mainly come from or lie and you can prevent them in the future.
- You collect data that can be used for quality analysis: With a good system, you register all deviations and improvements that are reported within your organization. This way you collect data that you can use for reports that can give you more insight into possibilities and problems. When you use all data correctly, you can monitor your progress and get a clear picture of where you stand in your quality improvement process. Not only do you ensure transparency in your quality management, but you also get full control over all registrations and their progress.
- You increase the clarity and efficiency of your quality processes: As mentioned earlier, quality management is strongly linked to Business Process Management. This is because with quality management you also look at processes; namely quality processes. By registering, analyzing, monitoring and improving deviations and improvements, you create the opportunity to also improve your quality processes. When everyone works with a quality management system and can immediately register and process improvements, you also increase the efficiency of individual employees and performance. This ultimately makes your quality processes many times more efficient, reduces costs, time and complaints and creates space to innovate.
- You create a process-oriented approach: By approaching your quality management with the process as a starting point, you work in a process-oriented manner. Processes are often connected to each other and something that happens in one process can therefore very well have an effect on other processes. You can look at possible risks in processes, which processes can be made more efficient and who is responsible or has tasks within certain processes. By working in a process-oriented manner, you see your organization as a whole of business processes. A quality management system helps you to visualize this.
- You create a culture for continuous improvement: When you implement a quality management system within your organization, this also involves a switch in your culture. It is necessary to ensure that everyone within your organization looks at the quality of their services or products in the same way. What you want is for everyone to be motivated to actually improve the quality and a pleasant culture that stimulates this plays a major role in this. It is therefore important that during the implementation everyone in your organization is clearly informed, learns to work well with the system and sees its value. Of course, good guidance is needed for this.
Quality system ISO 9001
When it comes to quality management, there is one standard that immediately stands out; the ISO 9001. With a good quality management system, it will not be difficult for your organization to be certified for the ISO 9001. When everything is properly arranged according to the rules, something that you can easily achieve with a good quality management system, you can request an audit in no time.
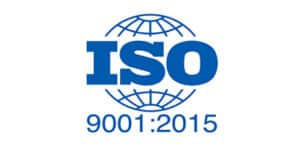
Read more about the ISO 9001 here:
ISO 9001
From the PDCA cycle to the PMMI cycle
Many consultants or professionals in this field will say that the PDCA cycle (Plan, Do, Act, Check) is very important within a quality management system. The PDCA cycle is generally the basis for continuous improvement, an important part of quality management that we discussed earlier. This cycle provides a structure for how best to handle and go through processes; this helps to systematically integrate continuous quality improvement into the working method and ultimately into your culture. However, at INBISCO we are more of our adapted PDCA cycle; the PMMI cycle (Plan, Manage, Monitor, Improve). We believe that with the PMMI cycle employees get more independence and responsibility within processes, instead of just being told what to do and being checked. Management also gets a more important role with the PMMI cycle. By focusing more on monitoring and improving in a quality management system, you get more focus on feedback and continuous improvement. As a result, you not only do what is necessary, but you really improve.
Read more about our quality management system here:
INBISCO Quality
Our quality management system
The word has been said a lot in this article, but finally we will talk about our own
quality management system. At INBISCO we have been working for years to perfect our management systems and to support organizations with our knowledge and expertise to take their quality management to a new level. We have succeeded in this, with some pride of course. Because we work closely with our partners, we have been able to implement many desired requirements and functions in our system that make it even easier for organizations to obtain ISO certifications. This personal approach not only makes our software the best quality management system in the sector, but also ensures that you can get the most out of your organization.
Interested?
Interested in our software and what we can do for your organization? Request a free demo or contact us and we will get back to you soon.