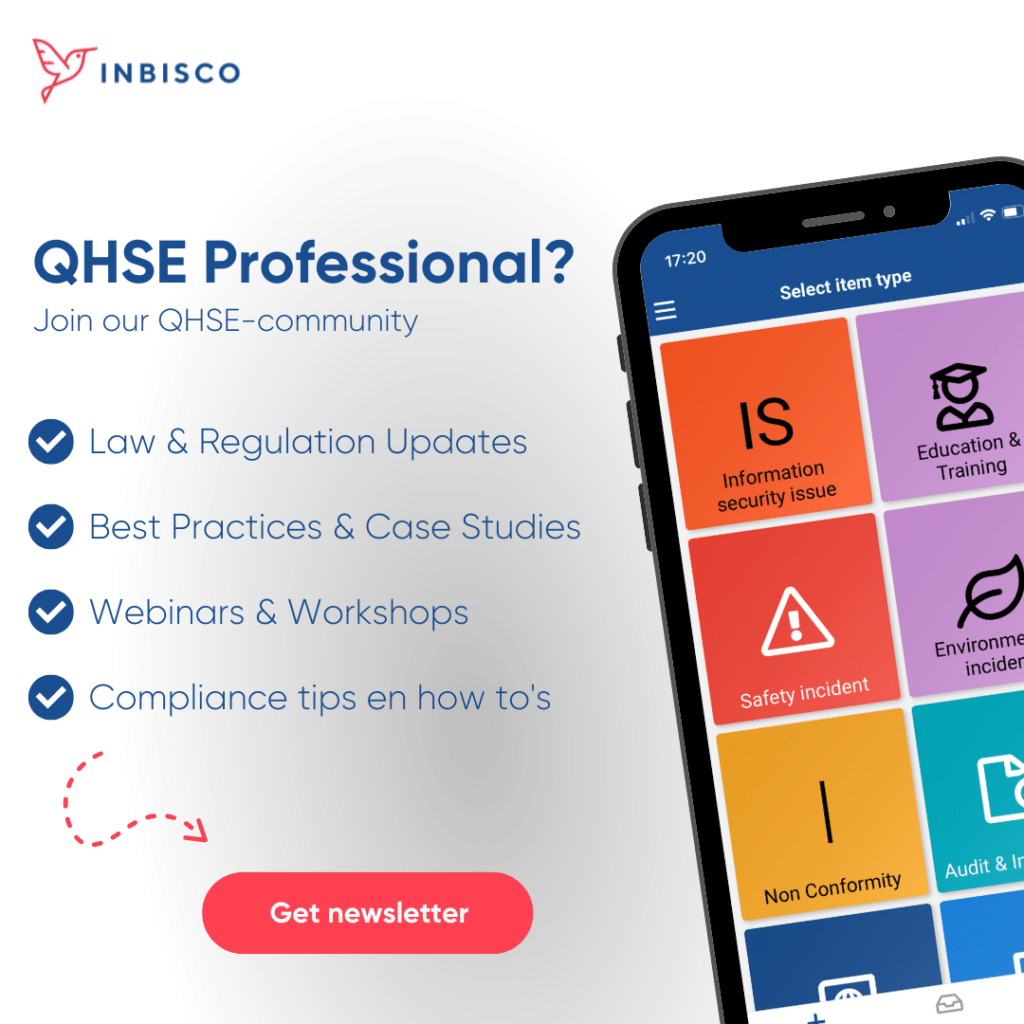
INBISCO QHSE Community
8 Oct 2024
Risk Inventory & Evaluation (RI&E) is a crucial process for organizations to ensure that their work environment is safe and healthy for employees. However, performing an effective RI&E can be a challenging task.
Risk Inventory & Evaluation (RI&E) is a crucial process for organizations to ensure that their working environment is safe and healthy for employees. However, conducting an effective RI&E can be a challenging task, especially when it comes to collecting and analyzing data, identifying risks and drawing up appropriate measures. Fortunately, INBISCO’s process and quality management software offers a valuable solution. In this article, we will discuss how the software can support organizations in conducting RI&E. We also share useful examples and a plan of action.
RI&E stands for Risk Inventory & Evaluation. It is a method that organizations use to identify and assess potential risks in their working environment. This involves looking at the hazards that are present and the likelihood that these hazards could actually cause harm. By carrying out a RI&E, organisations can better understand the risks and take measures to prevent or reduce them.
RI&E is not only important, but also mandatory for organizations. In the Netherlands, for example, the Working Conditions Act requires employers to carry out a RI&E and draw up a plan of action to address the risks. This obligation exists to ensure that employees can work safely and healthily. By carrying out a RI&E and taking the necessary measures, organizations can meet this legal obligation and at the same time ensure the safety and health of their employees.
Using INBISCO software, organizations can set up a central database to store all relevant information regarding RI&E. This includes data on the work environment, processes, working hours, safety measures, health risks and more.
By having all information in one place, organizations can easily collect, update and analyze data, making the RI&E process more efficient and streamlined.
Below are some examples of how a fictitious organization, using INBISCO Secure software, creates a successful plan of action.
Provide a detailed overview of all relevant risks within your company. Think of risks such as machine accidents, exposure to hazardous substances, noise, fire hazards and ergonomic problems.
Example:
Suppose you work at a production company. You can then use INBISCO Secure to collect information about all machines and equipment used in the factory, such as presses, cutting machines and welding equipment. In addition, users of the system can collect information about the materials used, such as chemicals and metals.
Identify potential risks based on your inventory. Involve employees in this process, as they can provide valuable insights into daily operations.
Example:
In the manufacturing company mentioned above, employees can be involved in identifying risks. For example, they can identify potential hazards such as the risk of cuts from sharp edges of metal parts, the risk of exposure to hazardous chemicals when mixing chemicals, and the risk of falls when working on elevated platforms.
Use the risk matrices and evaluation features in INBISCO Secure to assess the severity and likelihood of each risk. Apply automated algorithms to quantify and categorize the risks, giving organizations a better understanding of the most important areas of concern. Prioritize the risks based on this evaluation.
Example:
The manufacturing company can use the risk matrices to assess the risks. They can determine the severity of the risk based on the potential harm it can cause, for example, from minor injuries to serious bodily harm. They can also assess the likelihood of each risk based on the frequency or chance of the risk occurring.
Based on the risks assessed, define appropriate preventive measures.
Example:
For the manufacturing company mentioned above, they can establish preventive measures to control the risks identified. For example, to reduce the risk of cuts, they can require the use of safety gloves and cut-resistant clothing. To reduce the risk of exposure to hazardous chemicals, they can implement strict adherence to safety procedures and the use of personal protective equipment (such as respirators and safety glasses).
Monitor the progress of the measures taken and to evaluate their effectiveness. Schedule regular checks and audits to ensure that the risks are adequately managed.
Example:
The manufacturing company uses INBISCO Secure to perform audits and checks to ensure that the preventive measures are effective. They can perform inspections to check whether employees are complying with the prescribed safety measures, such as wearing personal protective equipment. They can also evaluate the effectiveness of the measures by, for example, analyzing accident reports and assessing whether there has been a reduction in incidents related to the risks identified.
By following these steps and using INBISCO’s process and quality management software, you can use a structured and effective approach when performing a RI&E. This helps identify and manage risks, resulting in a safer and healthier working environment for employees. Want
We can record and disclose the principles relating to safety via INBISCO- Secure. The established Information Security strategy outlines the policy and preconditions for a safe working method. Taking these preconditions into account, the working method is recorded in the Information Security Management System (ISMS) by means of processes and work instructions, in combination with all relevant (policy) documents. Processes and documents are now securely stored in the ISMS and can be easily shared with the organization.
Want to know what INBISCO – Secure can do for your organization?
Here you will find our latest blogs, events, online demonstrations and customer stories. Stay up to date with the latest developments and be inspired by practical examples in the field of quality, health, safety and environment.